Methyl acrylate (MA), one of the most important monomers, is widely used in the field of polymer materials, paints and coatings, textiles and adhesives production. The traditional methods are the acrylonitrile hydrolysis (ACH) process and propylene oxidation route followed by esterification. In recent years, with the depletion of petroleum resource and strict requirement of environmental protection, the production of MA from methyl acetate (MAE) and formaldehyde (FA) (or trioxane) at 623 K-653 K via one-step aldol reaction has been paid attention to. The yield and selectivity could reached up to about 70 % and 95 % when using VPO catalysts. However, the catalytic activity declines sharply after 24 h. Cs-P catalysts are more stable than VPO, while the yield only attains about 40 %.
The thermodynamic calculation results reveal that such reaction could proceed at low temperature (<100℃). According to the previous researchers’ work, the one-step and in-situ catalytic strategy is developed and demonstrated for preparation of MA from MAE and trioxane via one-step aldol reaction at 293 K (Fig 1). In addition, the yield can be obtained as 80.8 % with the selectivity of 94.4 %.

Fig 1. Mild catalytic synthesis of MA via one-step aldol reaction
The reaction mechanism is proposed and determined as Fig 2. Relatively moderate basic i-Pr2EtN is adopted in combination with Bu2BOTf to promote the enolization of methyl acetate. Meanwhile, trioxane can be depolymerized into FA with the in-situ catalysis of Bu2BOTf. In addition, the aldol condensation between enolate and depolymerized FA is also in-situ catalyzed by the generated [i-Pr2EtN-H]+[TfO]- ionic liquid, which is confirmed by deuterium labelled experiments.
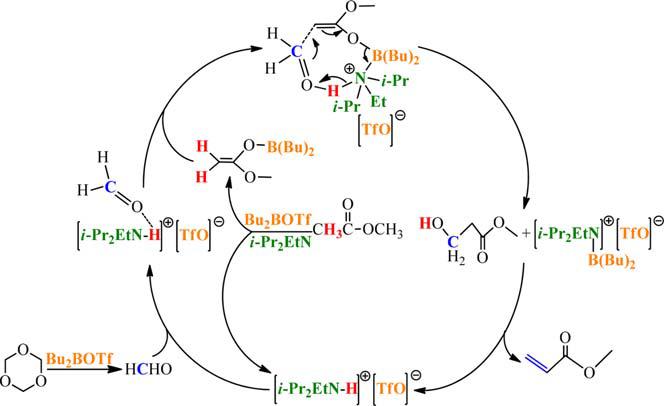
Fig 2. The proposed in-situ catalytic mechanism of MA synthesis
A complex interval micro-reactor system combined with following separation process are designed as Fig 3 to enhance the production efficiency. The simulation results indicate the solvent CH2Cl2, FA and MAE can be completely recovered from column 1. The main product MA will be collected from the top of column 2 with purity of 99.9 %, which meets the requirement of commercialization. The remained trioxane, Bu2BOTf and i-Pr2EtN can be also recycled from column 3 with a little of MA. These recovered materials will be mixed with the fresh one to form the optimal reactant composition. Then the mixture is equally divided and introduced into each interval micro-reactor for MA preparation, and the product separation process proceeds again as noted above.
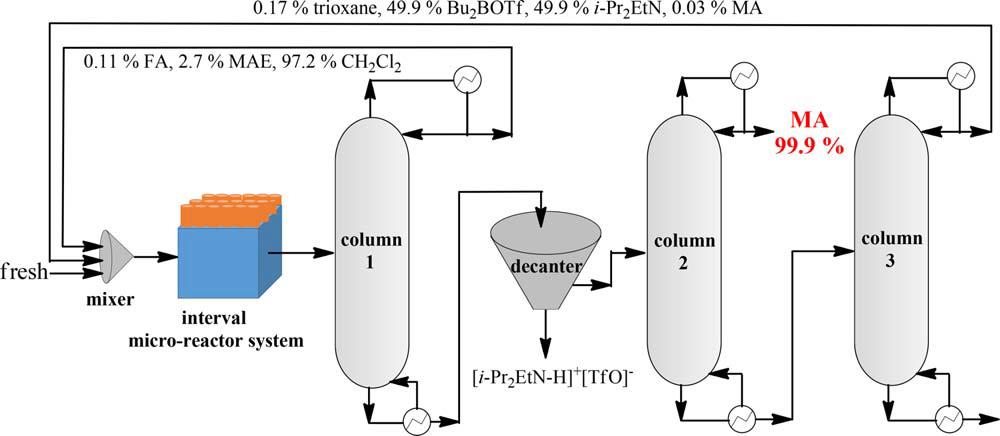
Fig 3. Reaction process design and product separation simulation
The research is supported by National Key Projects for Fundamental Research and Development of China (2016YFB0601303), National Science Fundation for Excellent Young Scholars (No. 21422607).
Their work entitled “Studies on mild catalytic synthesis of methyl acrylate via one-step aldol reaction” has been accepted by AIChE J., Doi: 10.1002/aic.16022.
http://onlinelibrary.wiley.com/doi/10.1002/aic.16022/epdf
Media Contact:
YUAN Pei
International Cooperation Office, Institute of Process Engineering, Chinese Academy of Sciences, Beijing 100190, P. R. China.
E-mail: pyuan@ipe.ac.cn
Tel: 86-10-82544882