Gas–liquid–liquid dispersions in stirred tanks are very common industrial operations used in chemical industry. Typical applications include hydroformylation, hydrogenation, liquid–liquid extraction and so on.
Previous investigations concerning the gas–liquid–liquid dispersions were mainly focused on the minimum agitation speed for complete liquid–liquid dispersion, gas absorption rate, and homogeneous biphasic catalytic aspects.
Researchers with Institute of Process Engineering (IPE) recently made process on gas-liquid-liquid macro-mixing in agitated vessels. Highlights of the results are that mixing time in gas–liquid–liquid and liquid–liquid stirred reactors is determined. High gas flow rates enhance macro-mixing while low gas flow rates damp it. Low oil holdups increase macro-mixing intensity while higher holdups decrease it. Axial impeller is more energy efficient than radial impeller.
The schematic diagram of experimental setup is shown in Fig.1. Experiments were carried out in a semi-batch manner. Air and tap water were adopted as the gas phase and the continuous phase, respectively. Three different liquids (kerosene, paraffin oil and methyl silicone oil) were used as the dispersed oil phase. The study concentrated on relatively low dispersed oil phase holdups and gas flow rates. The stirring speeds were tested for axial impellers.
Mixing time was determined by means of the electrical conductivity method using a pulse technique in this work. Studies focused on the effect of probe and injector positions, effect of agitation speed, effect of oil volume fraction, effect of gas holdup, effect of property of dispersed phase and so on. Results indicated that the mixing time in the gas–liquid–liquid system was similar to that in a liquid–liquid system. Gas aeration damps the macro-mixing process of the continuous phase at low aeration rates, and enhances the mixing efficiency at higher gas flow rates.
The power consumption was measured by a shaft–torque method. According to the comparison with the mixing time and the effect factors of it, researchers concluded that the power consumption decreased with the increasing dispersed oil phase volume fraction both with and without aeration and also fell with the increase of gas flow rate.
The combination of mixing time and power consumption analysis showed that the axial impeller is more energy efficient than the radial impeller. Besides, experiment data signified that the aeration and the dispersed oil phase influence the continuous phase mixing time in a complicated way. Based on a widely-used single-phase model, a new correlation for the liquid phase mixing time in gas–liquid–liquid three-phase stirred reactors was creatively proposed. The paper will tell more in Chemical Engineering Science.
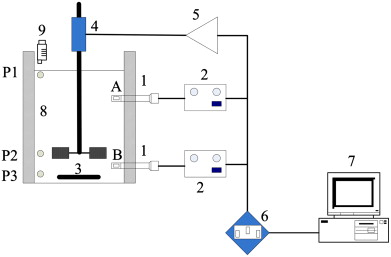
Fig. 1. Experimental setup. 1. conductivity electrode, 2. conductometer, 3. sparger, 4. rotary torque transducer, 5. amplifier, 6. data collector, 7. computer, 8. stirred tank, 9. injector. A (Probe A): 0.192 m from bottom and 0.115 m from shaft axis; B (Probe B): 0.03 m from bottom and 0.115 m from shaft axis; P1 (injector 1): at the liquid surface and 0.115 m from shaft axis; P2 (injector 2): 0.08 m from bottom and 0.115 m from shaft axis; P3 (injector 3): 0.03 m from bottom and 0.115 m from shaft axis.(image by IPE)